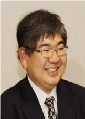
Shinji Hirai
Muroran Institute of Technology, Japan
Title: Creation of Keratin Resin and Fibroin Resin Using Fibrous Animal Waste Products
Biography
Biography: Shinji Hirai
Abstract
Keratin resin and fibroin resin have been prepared from silk or hornet silk powder, composed of fibroin protein, and from wool or chicken feather powder, composed of keratin protein, respectively, by heating at 100–180 °C under pressures of 20–40 MPa. The mechanically ground powders of wool waste or chicken feathers and pulverized waste silk, all of which are waste materials, can be used as the raw materials. In the case of wool, woven wool fabric also serves as a raw material after removal of the cuticle layers. For resinification, the powder was simply placed in a jig; in the case of woven fabric, it was stacked into the jig after punching to the size of the jig and was then heated under pressure using a hot press. The resins derived from silk or wool powder showed glass transition temperatures close to 200 °C and three-point bending strengths and flexural moduli superior to those of polycarbonate resins. On the other hand, the resin derived from wool powder had a very small expansion coefficient, with a value comparable to metals such as copper or aluminum. Moreover, the three-point bending strength of the resin derived from woven wool fabric increased to 116 MPa. Furthermore, upon applying stress to the resin, reversibility to woven fabric was observed, resulting in excellent impact resistance that is superior to that of ABS resin. Compared to the resins derived from wool and silk powders, the resin derived from chicken feather powder had a lower glass transition temperature and a larger thermal expansion coefficient, whereas the three-point bending strength, the elastic modulus, and the Vickers hardness were found to be lower. However, with the sole exception of the inferior three-point bending strength, the other features of this resin were comparable with those of polycarbonate.