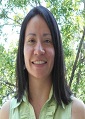
Andrea Arias
Corbion Purac BV, The Netherlands
Title: Polyethylene furanoate performance as a barrier material in multilayer bottles
Biography
Biography: Andrea Arias
Abstract
Poly(ethylene furanoate) – PEF has gained extensive attention in recent years due to its high barrier properties to oxygen and carbon dioxide [1]. PEF is a biobased polyester polymerized through combination of 2,5-furandicarboxylic acid – FDCA and ethylene glycol. Many authors consider PEF a potential replacement to PET and the next generation of FDCA biobased polyesters [2]. The successful introduction of PEF in the beverage and food packaging industry requires bringing concrete proof of its applicability and versatility as a barrier layer, combining the fundamental understanding of the unique properties of PEF with the more practical aspects of the tailored application development [3,4]. The clarity and mechanical performance of PET have placed it as the material of choice for manufacturing of
packaging for carbonated soft drinks (CSD) juices and water. Multilayer packaging has been developed under the principle to sandwich a high barrier material between PET layers in order to improve its undesirable low barrier to CO2 and O2 – often a limitation of PET containers [5]. In this talk the barrier enhancement properties of multilayer bottles using PEF as an intermediate layer embedded in a PET CSD bottle will be presented. The manufacturing of preforms and bottles was accomplished using two-stage injection stretch blow molding –ISBM. The weight percentage range of PEF in the bottle preform was defined at 3, 5, 10 and 15wt% and PET monolayer was used as a reference. The CO2 permeation of multilayer PET/PEF bottles was studied over time under standard conditions, i.e. 22°C and 50% RH. Table 1 shows the barrier improvement factor for each multilayer composition, which is calculated as the ratio between the loss percentage per day using the monolayer PET as a reference. At the highest PEF wt.% studied, i.e. 15wt%, the PEF medium layer contributes to CO2 loss twice slower than PET monolayer bottles. For the same concentration, the barrier to O2 is improved by 70%, as it is depicted in Table 2. In addition to CO2 and O2 barrier performance, the relevant aspects to the processing of PEF in typical pilot facilities involving the flow viscosity properties, temperature processing windows and melt stability will be discussed as well.
Table 1 – Carbon dioxide barrier improvement factors of multilayer PET/PEF bottles
Bottle |
CO2 loss(%/day) |
BIF |
100% PET |
0.223 |
1.00 |
3wt% PEF |
0.175 |
1.27 |
5wt% PEF |
0.147 |
1.54 |
10wt% PEF |
0.125 |
1.80 |
15wt% PEF |
0.107 |
2.08 |
Table 2 – Oxygen barrier improvement factors of multilayer PET/PEF bottles
Bottle |
O2 gain (ppm/day) |
BIF |
100% PET |
0.052 |
1.00 |
3wt% PEF |
0.044 |
1.19 |
5wt% PEF |
0.040 |
1.30 |
10wt% PEF |
0.035 |
1.46 |
15wt% PEF |
0.031 |
1.68 |